Welcome to our injection molding news blog, focused on just that… injection molded manufacturing for plastics products.
From industry news, to company news here at HTI Plastics, we work hard at giving you the best articles, news and advice within our injection molding news blog. Be sure to visit our other sister companies, Lincoln Plastics, a leader in extrusion molded products, and Apex Plastics, a leader in blow molding manufacturing of containers and juice bottles, and many more bottle options.
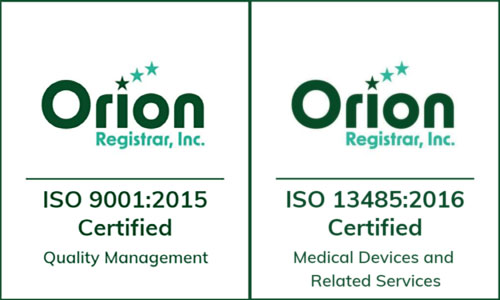
Re-Certification for ISO 9001:2015 and ISO 13485:2016
Lincoln, NE - HTI Plastics, a leading injection molding manufacturing company, is proud to announce our achievement of re-certification for ISO 9001:2015 and ISO 13485:2016, underscoring our dedication to maintaining the highest standards of quality and compliance...
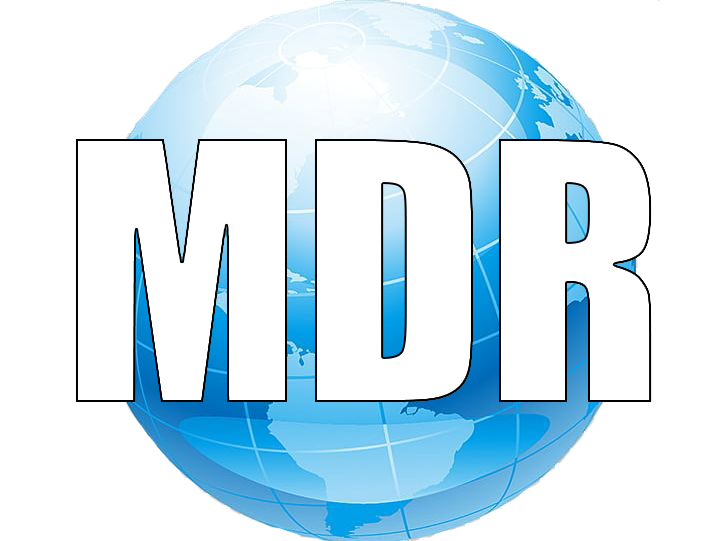
HTI Plastics Received MDR Certification to produce CE and CA devices
Lincoln, NE - HTI Plastics, a world leader in injection molded plastic parts, has been producing pharmaceutical applicators in the feminine hygiene market for over thirty (30) years. For a majority of 2023 our quality and engineering departments worked diligently on...
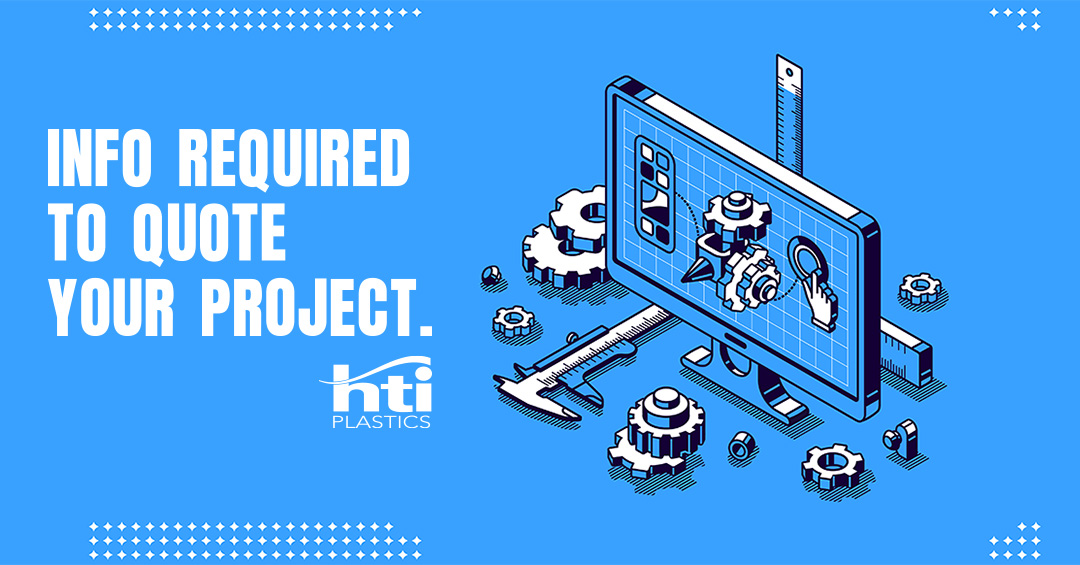
Information Required to Quote Your Plastic Project
Today we will take a look at the information required to quote your plastic project. Often customers and prospects needing plastic injection molded products and solutions come to HTI with an idea and a vision. Many of these companies know what they want in the end but...
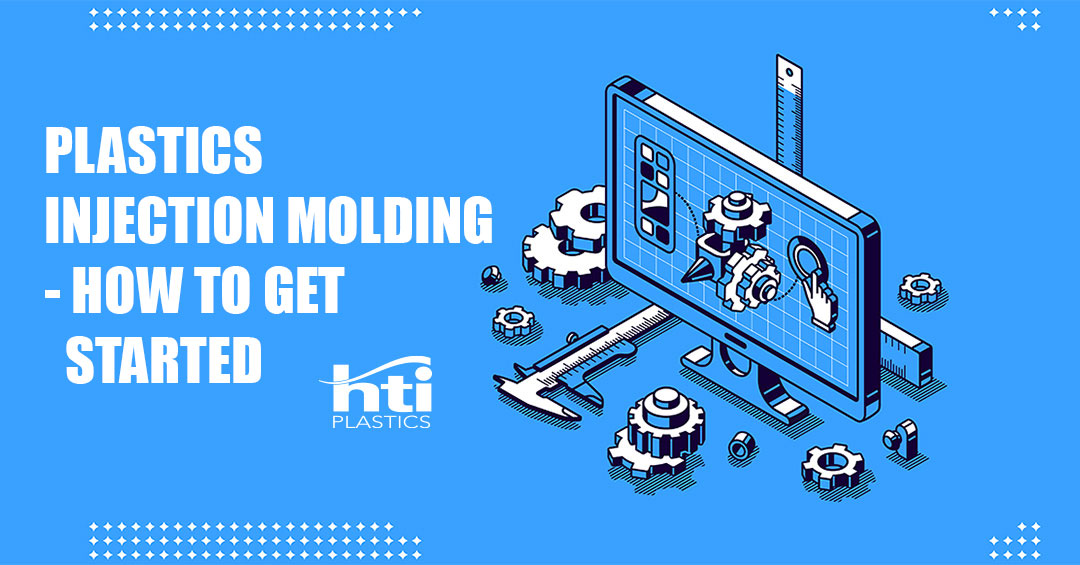
How to get your Injection Molded Plastics Project Started
Welcome to the second edition of our Basics of Injection Molding blog series. In this edition we will look at what the next steps are in moving forward with an injection molded plastics project. What do you do, where do you go, what questions should you ask? Those...
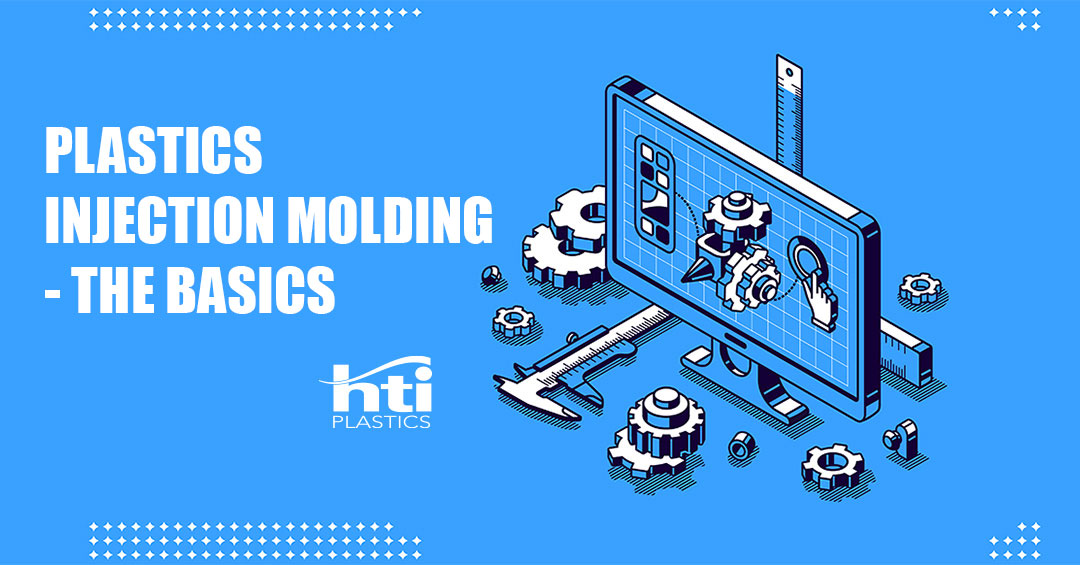
Plastic Injection Molding – The Basics
Welcome to the HTI Plastics Basic Principles of Injection Molding Blog series. In this series we will look at topics related to the basics of this type of manufacturing responsible for so many products we used every day. We will examine, topics such as a general...
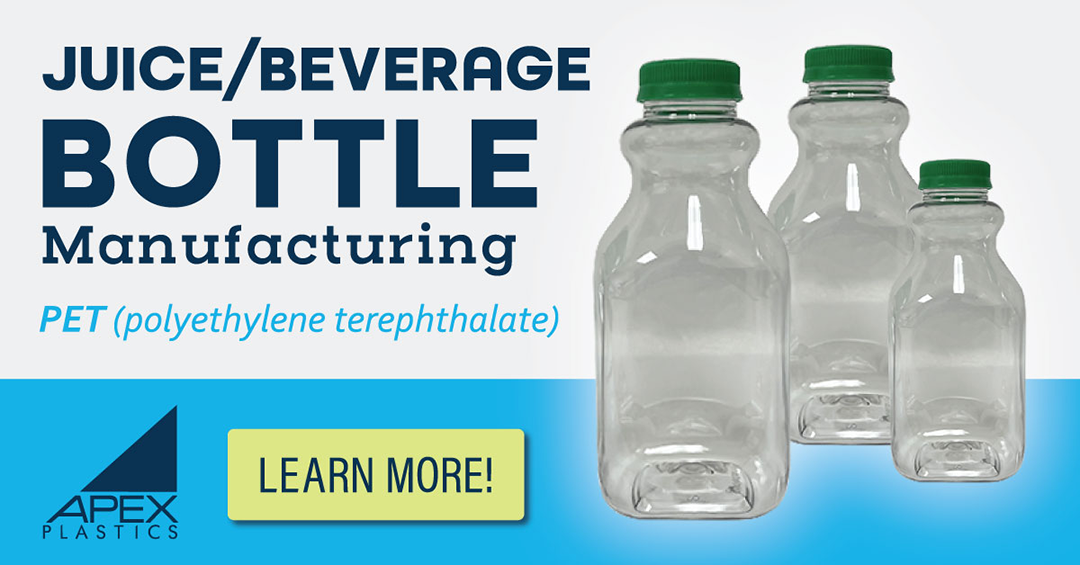
Sister company, Apex Plastics offers PET Juice/Beverage Bottle Mfg.
As a professional blow molding company, our sister company, Apex Plastics, in Brookfield Missouri offers high quality PET Juice/Beverage Bottle manufacturing. Apex Plastics offers 4 size options, including 8oz, 16oz, 32oz, and 59oz bottles. One thing unique about Apex...
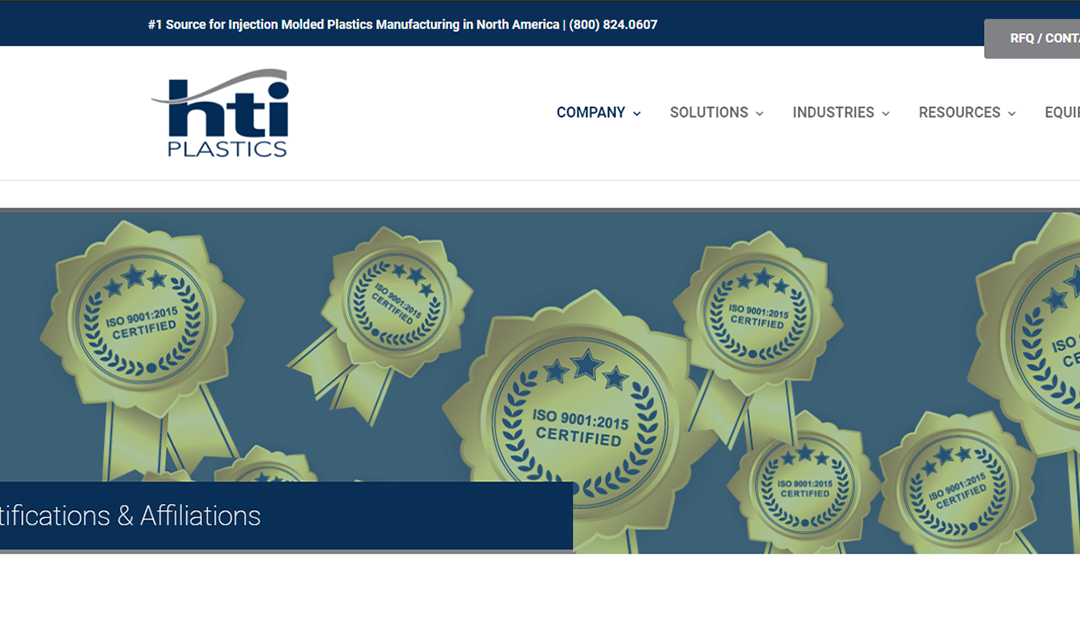
ISO Registrar conducted their 2023 Surveillance Audit of HTI Plastics
In February of 2023, our ISO Registrar conducted their 2023 Surveillance Audit of HTI Plastics with no major or critical findings. The auditor noted in the report HTI’s “excellent use of metrics and analysis” with a “very mature and stable Quality Management System to...
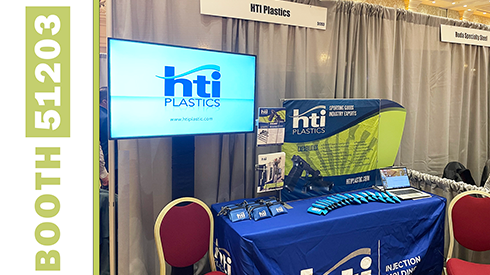
HTI Plastics at Supplier Showcase (Shot Show ’23)
Come visit us at Booth 51203, Monday and Tuesday, as HTI Plastics is again a Show Show Firearms Manufacturer located in Lincoln Nebraska. THE VENETIAN 5TH FLOOR PALAZZO BALLROOM Meet with 500+ suppliers offering countless materials and solutions for your manufacturing...
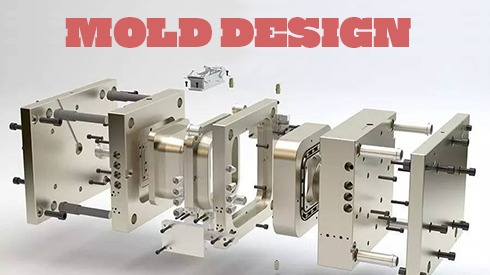
Quality Mold Design for Manufactured Products
Quality Mold Design. In order to repeatedly make a high-quality molded part, all of the key inputs have to be considered – part design, material selection, mold design, and establishing a robust process. At HTI Plastics, we consider all of these elements on a new...